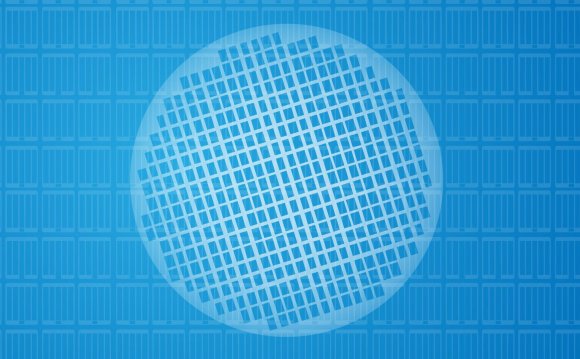
Training, Other Qualifications
People interested in becoming semiconductor processors—either operators or technicians—need strong technical skills, an ability to solve problems intuitively, and an ability to work in teams. Mathematics, including statistics, and physical science knowledge are also very useful. Communication skills and an understanding of manufacturing principles are also very important.
To ensure that operators and technicians keep their skills current, employers provide regular on-the-job training. Some employers also provide financial assistance to employees who want to earn an associate or bachelor's degree, especially if the employee is working toward becoming a technician.
Workers advance as they become more comfortable with the equipment and better understand the manufacturing process. Employees train workers for several months, after which they become entry-level operators or technicians. After a few years, as they become more knowledgeable about the operations of the plant, they generally advance to the intermediate level. This entails greater responsibilities. Over time, usually 7 to 10 years, workers may become senior technicians, who lead teams of technicians and work directly with engineers to develop processes in the plant.
Education and Training
For semiconductor processor jobs, employers prefer applicants who have completed an associate degree. However, experience plus completion of a 1-year certificate program in semiconductor technology, offered by some community colleges, may also be sufficient. Some semiconductor technology programs at community colleges include internships at semiconductor fabricating plants. Other applicants may qualify by completing a degree in high-tech manufacturing. Hands-on training is an important part of degree and certificate programs.
Other Qualifications
This career requires strong written and verbal communication, and teamwork skills. Since some semiconductor processors work with intricate equipment they must have previous good mechanical experience.
Nature of the Work
Watch this video to see what it is like to work at a manufacturing company that makes semiconductor components.Semiconductors are unique substances, which, under different conditions, can act as either conductors or insulators of electricity. Semiconductor processors turn one of these substances—silicon—into microchips, also known as integrated circuits. These microchips contain millions of tiny electronic components and are used in a wide range of products, from personal computers and cellular telephones to airplanes and missile guidance systems.
To manufacture microchips, semiconductor processors start with cylinders of silicon called ingots. First, the ingots are sliced into thin wafers. Using automated equipment, workers or robots polish the wafers, imprint precise microscopic patterns of the circuitry onto them using photolithography, etch out patterns with acids, and replace the patterns with conductors, such as aluminum or copper. The wafers then receive a chemical bath to make them smooth, and the imprint process begins again on a new layer with the next pattern. A complex chip may contain more than 20 layers of circuitry. Once the process is complete, wafers are then cut into individual chips, which are enclosed in a casing and shipped to equipment manufacturers.
The manufacturing and slicing of wafers to create semiconductors takes place in cleanrooms—production areas that are kept free of all airborne matter because the circuitry on a chip is so small that even microscopic particles can make it unusable. All semiconductor processors working in cleanrooms must wear special lightweight outer garments known as "bunny suits". These garments fit over clothing to prevent lint and other particles from contaminating the cleanroom.
There are two types of semiconductor processors: operators and technicians. Operators start and monitor the equipment that performs the various production tasks. They spend the majority of their time at computer terminals, monitoring the operation of equipment to ensure that each of the tasks in the production of the wafer is performed correctly. Operators may also transfer wafer carriers from one station to the next, though the lifting of heavy wafer carriers is done by robots in most new fabricating plants.
RELATED VIDEO
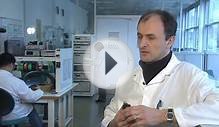
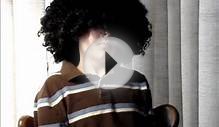
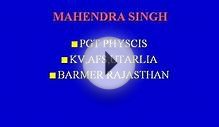